Managing Risk to Lower Insurance Cost
Managing Risk to Lower Insurance Cost
By now you know that everyone at ArboRisk is a full on risk management nerd. And for good reason, by helping our clients practice risk management, we ensure they are doing everything they can to operate safely and efficiently to send every employee home safe each night.
But one of the greatest side effects of proper risk management is lowering the cost of your insurance coverage. This is achieved up front during the insurance quoting process and over the long term with a reduction of injuries and accidents.
I want to address three categories of risk management that can help you lower your insurance cost and to encourage you to think about your business through the lens of an insurance company the next time you’re getting an insurance quote. Similar to showing a bank your business plan for a loan, you have the opportunity to show an insurance company why you’d be a good risk for them and why they should give you lower rates.
Employee Management
We’re all aware that employee management is the key to running a successful business. Employee management starts with having a sound hiring and onboarding process. This shows an insurance company you are dedicated to hiring and retaining the best employees.
Employee management doesn’t end with the onboarding process. Insurance companies also want to see a tree service that has systems for continuing to monitor their employees. Performing background checks, drug tests (DOT and post-accident), motor vehicle record checks, and continuing education audits are all examples of ways you can manage your employees after they are hired.
Company culture is the last area I want to discuss regarding employees. Why would an insurance company care about your company’s culture? Simple. Turnover. The most successful tree services have the strongest company cultures. A strong culture reduces turnover by keeping employees committed to your team and ultimately leads to less accidents for an insurance company to cover.
When looking to improve your employee management, ask yourself these questions.
1) Do you have a formal application and interview process?
2) Do you utilize a skill proficiency/competency checklist?
3) In what ways are you monitoring your employees?
4) How loyal are your employees to your company?
Safety & Training
While one can argue that safety and training fall under the employee management section, in the tree care industry it is just too important to hide within another section. Job site safety and employee training is obviously one of the most important pieces to a successful risk management program and therefore the first place you should look at to help minimize your insurance costs.
In the simplest form, there are three risk management items you need to have for safety and training within your company; a written safety program, documentation of safety training meetings and a written injury reporting procedure.
These core documents should be sent to your insurance company as proof of how you are managing safety and training at your company as the ultimate way to get the best rates…you guessed it: Having great documentation and great loss history!
In addition to the written policies mentioned above, obtaining industry credentials (think ISA Certified Arborist or TCIA Accreditation) is another way to show the insurance companies that you are committed to bettering your business and therefore lowering the risk of injuries and accidents. In fact, many insurance companies are requiring this before they even quote the coverage. If your company has done the leg work to obtain industry credentials, make sure the insurance company knows it and what that credential entails.
Ask yourself these safety and training questions:
1) Do I have written programs for safety, training and injury reporting?
2) Can I easily prove the safety training that my team members receive?
3) Is there a regular schedule to the training within the company?
4) How do the industry credentials that my company and team have lower the chances of an accident?
Fleet Management
Second to your workers’ compensation premium, your business auto insurance is probably the next most expensive policy. Throughout the tree care industry, auto claims are on the rise, both in numbers and dollars paid out, which is why you’ve likely seen an increase in your auto insurance renewal pricing. Implementing risk management procedures with your fleet can put you back in control of the increasing premiums.
Risk management within the fleet requires looking at both your drivers and your vehicles. A simple tactic that you can employ for your drivers is to create a driving test. This ensures they are qualified to drive the vehicles you need them to safely before tossing them the keys to take the truck to the jobsite.
For the vehicles, I’d encourage you to look into a fleet management software either directly through your insurance company or through a third party. This will not only give you a way to track maintenance of each vehicle, it will also give you valuable data on how and where the vehicles are being driven. The data that you can obtain from the software will help you and your insurance agent negotiate for lower business auto insurance costs.
Here are some questions to ask yourself in regards to your company’s fleet management program:
1) How are the driving records of my employees? Are they reviewed? How often?
2) Do employees need to pass company standardized driving tests?
3) Do I have detailed fleet maintenance records?
4) Do we monitor our fleet when the vehicles leave the shop?
Lastly, I feel it’s important for you to understand that insurance companies need roughly 40% of your insurance premiums just to cover their operating expenses. That means that if you have over 60% of your premium paid out in claims, you’re likely not a profitable client for the insurance company. Helping the insurance company see what risk management tactics you are taking to limit your claims will be the proof they need to issue lower insurance premiums to you.
If you’re looking to implement a risk management mindset within your company, reach out to an Arborisk team member today to learn about our services including our Thrive program which gives you access to tree care industry consultants that can help you develop specific programs and procedures that you need to become extraordinary.
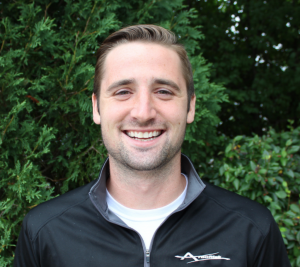
Written by: Malcolm Jeffris
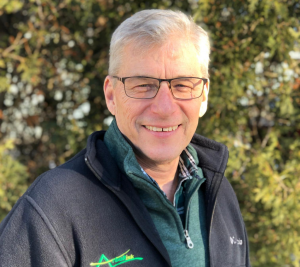
and Jim Skiera