3 Simple Steps to Creating a Culture of Safety
3 Simple Steps to Creating a Culture of Safety
No business owner wants to see their employees get hurt. The feeling is indescribable when one of your team members suffers an injury, no matter how large or small. Why is it then that so many business struggle to implement a culture of safety? I believe the main reason is that safety seems overwhelming. I want to give you 3 simple steps to grab a hold of that elusive culture of safety and begin to improve your business from the inside.
Ownership Commitment – The culture of any organization starts from the top. The owner and management must make a commitment to their team that working safely is preferred over working quickly. Understanding how safety pays off within your organization is critical. According to OSHA, an average muscle strain will cost the business almost $68,000 in direct and indirect costs! The small administrative cost and upfront expenses that you may have to spend to get the safety culture started are extremely minor compared to what happens when there is an injury.
Employee Engagement – Once this direction is set by the leaders of the company, they must make sure to get the employees aboard. The best way to do this is to establish a safety committee with representatives from all departments. Asking for volunteers is the most efficient way of getting the employees aboard with this. It is the Safety Committee’s job to lead by example when working safely, review or create the written safety policies, enforce the safety rules and act as the liaison between the front line employees and the management.
Open Communication – A culture of safety will not develop if the employees do not understand what is expected of them and given a platform to discuss any safety questions they have. The leadership of the organization must specifically state the intentions of the safety culture and allow for open communication regarding all aspects of safety. An employee must feel secure enough in his or her job that they can talk freely about a close call or near miss without fear of repercussion.
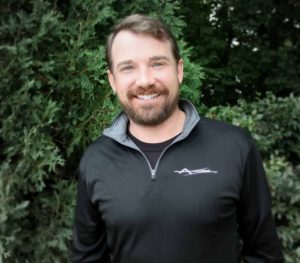
Written by: Eric Petersen
Recent Comments