Coronavirus Safety for Arborists
Coronavirus Safety for Arborists
By now, everyone has been inundated with information from the Centers for Disease Control and Prevention (CDC) regarding the Coronavirus, however, I have yet to see an article directly relating to the unique exposures that a tree care company has to the virus.
Unfortunately, many arborists are not that concerned with contracting the virus because they work outside and do not have much exposure to other people.
This can be a very dangerous attitude to take especially in an industry with a labor shortage, so I wanted to outline a few areas to consider within your tree care company to limit the spread of any illness throughout your entire team. These are, of course, in addition to the guidelines already posted by the CDC.
Are your company issued PPE’s actually personal? – If your safety equipment (specifically, helmets, eye protection, face shields, chaps, respirators) is not being assigned to a specific employee, now is the time to get out the Sharpie and start writing someone’s name on each piece.
Trucks – Place a container of sanitizing wipes in each truck and make a thorough wipe down of the interior of the cab (including the door handles, steering wheel, gear shifter, radio controls, door locks and window controls) part of your pre and post trip inspections.
Chainsaws and other Handheld Equipment – Just like the trucks, sanitize any hand held equipment after each new person uses the equipment and at the end of each day.
Video Conferencing – Utilize technology like Zoom or Webex to deliver your safety meetings and the morning crew duties and assignments to limit the amount of face to face interaction.
Electronic Proposal Delivery – Just like using technology to talk with your team members, implementing an electronic proposal delivery system helps minimize spreading germs directly to and from customers. It also has the added benefit of streamlining paper processing time for you office crew.
Remote Office – Speaking of your office crew, using a cloud based remote desktop server, your office team can be fully operational anywhere in the world. If you are not yet using a cloud server, hopefully the current situation we are in will give you added incentive to get one in place. It also will double as information security in case of a large loss at your office, like a fire or tornado.
By no means is this list all-inclusive, so take a few moments and think about every aspect of a team member’s day and how you can limit their exposure to germs inside your shop and out on the jobsite. Doing this will certainly reduce the risk of your employees contracting the virus at work.
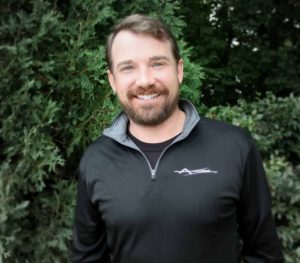
Written by: Eric Petersen
Recent Comments